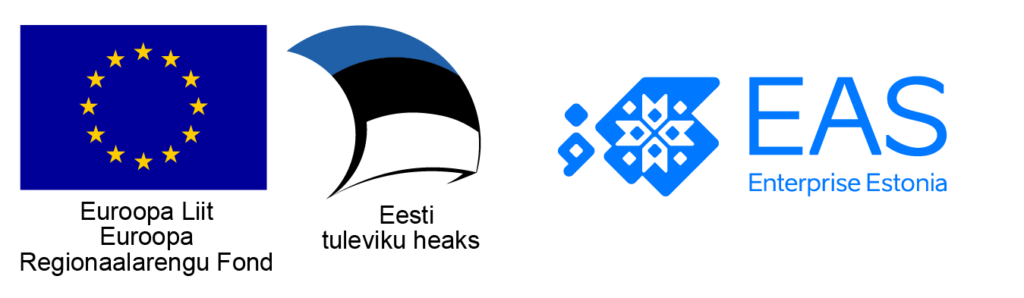
Brief description of project:
Unplanned downtime in a production company can take up as much as 38% of working time, amounting to up to 50 billion USD in financial damage per year. Many production processes are non-transparent, making it difficult to increase production efficiency.
Although many enterprises are already collecting data from production equipment, there is still no clear answer as to what happens before and after the equipment performs its function.
Because the production processes are non-transparent, production companies do not have a clear overview of the journey the materials and semi-manufactures take from warehouse to production and from one machine to another. The causes of problems and downtime are thus unknown and the process of identifying bottlenecks is complex and time-consuming. Products that are manufactured with the wrong specification due to non-transparent processes result in costly returns which also damage customer relationships.
Industrial companies need a real-time overview of the processes, which can be achieved with the use of digital twin technology. A real-time overview of production, as well as stock and trade flows, allows for increased operating efficiency and productivity.
Modern indoor and outdoor radio positioning technologies ultra-wideband (UWB) and GNSS RTK or GPS positioning allow such a system to be implemented in the best and most cost-effective way possible. By combining these two technologies, it is possible to create a system where positioning takes place across a wider area, including outside of production and storage facilities.
Project objectives:
Develop a hardware and software solution based on precise positioning technologies to promote the efficiency and productivity of both production and warehousing companies. The final product comprises UWB + GNSS RTK positioning network hardware and software adapted for industrial use, additional sensors and application software.
Project outcome:
- Digital warehousing via remote monitoring of products – the solution makes it easier to place and locate goods in a warehouse because the location of the goods and raw materials is traceable in real time, which allows the organisation of goods to be optimised, speeding up the process even more. As a result, the productive working time of employees and equipment is improved, increasing productivity by approximately 8–12%.
- Optimisation of the production process through the monitoring of people, equipment and raw materials – the solution makes production transparent, allowing inefficient activities to be identified and eliminated, downtime to be prevented, and the quality of the products to be monitored. Thanks to the solution, productivity can be increased by approximately 10–20%, including all operations from the delivery of raw materials to the dispatch of goods.
Duration of project: 01.02.2021 – 30.06.2023
Grant amount: EUR 499,990
Want to make your production more effective?
Atemix will get every factory into its best shape and help them keep it.