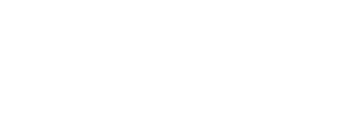
Mayeri Industries AS is the leading producer of laundry detergents and cleaning agents in the Baltics and is 100% based on Estonian capital. The product portfolio of Mayeri Industries includes 16 trademarks in four different product groups: household chemicals, automotive chemicals, garden chemicals, and solvents.
The flagship brand of the company established in 1889 by a Baltic German man, Richard Mayer, is the household chemicals brand Mayeri which embodies the core values of the company.
Their slogan ‘We care about you! We care about the environment!’ reflects the company’s vision of responsible production and products. Mayeri is convinced that laundry detergents and cleaning agents can be produced without harming the environment. They are, however, aware that not everything can be achieved at once – the implementation of cutting-edge technology in production is expensive. The company is moving towards cleaner production and more sustainable products on a step-by-step basis.
The challenge:
The washing powder dispenser line of the client is extremely outdated and so is the printed circuit board based PLC (PC) used to control it. The system frequently malfunctions, which causes problems in production. As part of the project, we designed the automation panel, created new controls and performed all the necessary assembly work.
The dispenser line was manufactured in 1994 and its control system is made up of antiquated components, making it either very difficult or outright impossible to find components in the event of a malfunction. Since the system often malfunctioned due to the automation components, but the mechanical and structural components of the device were high-quality and suitable for maintenance and repair, the client asked us to upgrade the automation system.
Our goal was to create a modern automation system with a long service life. To achieve this, we needed to analyse all the components of the device and determine which of those components were of critical importance and had to be utilised in the new system and which parts had to be done differently.
Work completed during the project:
Many hours of the project were spent analysing the device and all its components in great detail because some unusual solutions were used in its control system. Thus, it was important to understand exactly what had been done, why and how. Due to the unconventional design of the device, it was not possible to install a regular control panel on the floor. It was also not possible to install a surface-mounting panel with the required dimensions, so we had to install all the components of the control panel on a mounting plate which was then installed inside the old panel.
As a result of thorough analysis, all the necessary data was collected and a new automation system was designed, a control panel was built, a new PLC program was created, and a new HMI was programmed. Within a short period of time, all the necessary works on site were completed and the system was set up and put into use.
Result:
The new automation system was set up to utilise previously existing equipment and extend its service life. After the completion of the project, the system’s reliability improved, faults that had previously been a frequent concern disappeared, and the work process thus became smooth and stable. Thanks to the new program and control panel which we designed and implemented, the client can now contact us at any time and receive assistance quickly – this was not previously possible as the device had no on-site support.
Client: MAYERI INDUSTRIES AS, TABIVERE PRODUCTION PLANT
Area: CHEMICAL INDUSTRY
Work completed during the project:
- Collection of basic data
- Analysis of automation process
- Design of automation system
- Design and construction of automation control panel
- Assembly of unit
- PLC programming
- HMI programming
- System setup
- Drafting of documentation and sketches
Soovid oma tootmist efektiivsemaks muuta?
Atemixi tehaste doktorid viivad iga tehase tippvormi ja aitavad seda vormi hoida.